Тяжелая ситуация на рынке подтолкнула предприятия металлургического профиля в Ростовской области к участию в нацпроекте по повышению производительности труда. Это позволило им перестроиться, задействовав внутренние резервы
Производственный технопарк «Юг-Мет», расположенный в Аксайском районе Ростовской области, – это современный инфраструктурный комплекс, где на одной площадке размещены производственные цеха, складские помещения, логистический центр и офисные помещения. Резидентами технопарка являются более 10 компаний металлургической и ломоперерабатывающей отрасли.
В новых экономических условиях технопарк, как и другие участники нацпроекта «Производительность труда», нуждается в использовании всех резервов для обеспечения финансовой устойчивости. Эти резервы удалось найти после участия в программе бережливого производства.
Технопарк — целая индустрия
Задача технопарка – аккумуляция и поддержка производственных предприятий, ориентированных на выпуск достойных продуктов, востребованных металлургическим рынком, сообщается на его сайте. На территории размещены промышленные комплексы по переработке цветных металлов, предприятие по изготовлению медной катанки, завод по производству алюминиевого профиля, завод по выпуску энергосберегающих светодиодных светильников, а также покрасочные цеха и логистические центры. Точки по сбору сырья работают во всех крупных населенных пунктах Ростовской области и Краснодарского края.
Основная специализация технопарка – выпуск продукции цветной металлургии. Резиденты работают по многолетним контрактам с системообразующими российскими и транснациональными компаниями-потребителями сплавов цветных и черных металлов.
Участниками нацпроекта по повышению производительности труда в технопарке стали четыре компании: ООО «Донметсбыт», ООО «Металлпромсбыт», ООО «Коксовская профильная компания» (уже прошли программу внедрения бережливого производства) и ООО «Аксайский металлургический комплекс» (участвует в проекте сейчас).
Необходимость новых методов назревала давно
Понимание необходимости новых методов управления производством руководство предприятий осознавало и до участия в проекте. При поддержке Регионального центра компетенций (РЦК, оператор нацпроекта в Ростовской области) была проанализирована работа компаний, выбран поток создания ценности, в котором реализованы производственный анализ, 5S, стандартизированная работа, картирование и т.д. Каждый из инструментов позволил сделать бизнес-процессы компании более прозрачными, а также поменять отношение сотрудников к рабочим обязанностям.
Предлагаемые методики диагностики, компетентная экспертная оценка помогли достоверно проанализировать текущую ситуацию на производстве и наметить стратегию оптимизации. Программа обучения, которое прошли представители разных подразделений предприятий с, была направлена на внедрение инструментов бережливого производства, оптимизацию производственных процессов и создание инфраструктуры для внедрения культуры постоянных улучшений.
У «Коксовской профильной компании» для оптимизации был выбран поток изготовления профилей из алюминиевых сплавов методом экструзии. Профили составляют значительную долю в общем объеме производимой продукции. Выявили 33 ключевые проблемы. Для сокращения времени простоев оборудования и других производственных проблем разработали и внедрили цепочку помощи. Провели модернизацию электрического питания, чтобы исключить обрыв кабеля, который останавливал производство. Кабель заменили на шлейф закрытого типа. За полгода рабочей группе проекта удалось достигнуть всех поставленных целей. Для этого были выполнены ключевые задачи: проведено обучение сотрудников основам бережливого производства, внедрена система 5С на всех участках завода, внедрена и стандартизирована система всеобщего обслуживания. Снижено время протекания процесса на переналадку оборудования путем внедрения инструмента SMED. За шесть месяцев участия в нацпроекте Донской производитель алюминиевого профиля увеличил выработку на 13%.
По завершении активной стадии проекта был разработан комплекс мероприятий до 2024 года и сформулированы новые цели. В течение следующих 2,5 лет на предприятии планируют сократить время протекания процесса на 92%, сократить незавершенное производство на 90%, увеличить выработку на 39%. Для этого полученный в ходе обучения опыт будет масштабирован на все производство.
На «Аксайском металлургическом комплексе», который является одним из крупнейших российских заводов по производству медной катанки и алюминиевого профиля, в ходе начальной диагностики выявили 24 проблемы. После реализации проекта время протекания процессов и объем потребления газа снизились на 30%. Одной из главных проблем была излишняя обработка, технологию производства усовершенствовали, в результате чего сократилось время изготовления изделия.
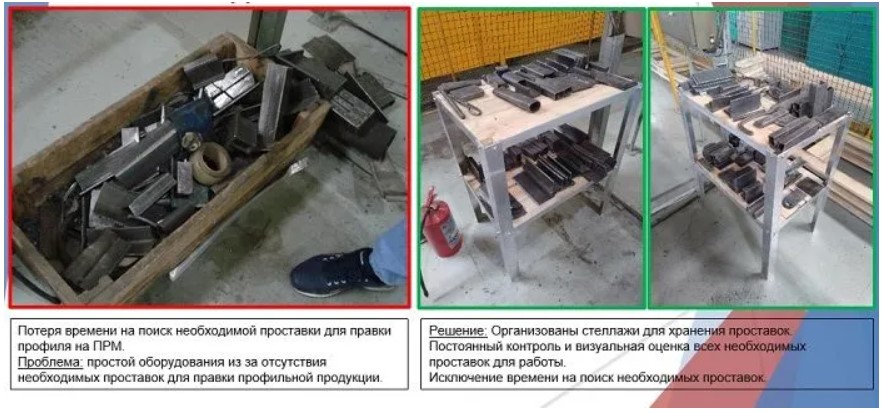
Для «Донметсбыт» участие в проекте позволило достичь следующих результатов в потоке заготовки и сортировки лома и отходов меди: сократить время протекания процесса на 14%, сократить запасы в потоке на 15%, повысить выработку на 9,2%.
ООО «Металлпромсбыт» с помощью инструментов бережливого производства в потоке заготовки и сортировки лома и отходов алюминия достиг схожих результатов: на 15% сократил время протекания процесса, на 12% — запасы в потоке и на 9% повысил выработку за смену.
ООО «Донметсбыт» и ООО «Металлпромсбыт» сохранили внедренные стандарты производства. ООО «Коксовская профильная компания» активно пользуется и развивает полученные инновации, претендует на получение льготного кредитования на развитие производства. ООО «Аксайский металлургический комплекс» еще в процессе реализации штатных мероприятий регионального центра компетенций, но уже есть понимание, что времени, отведенного на прямое взаимодействие, ввиду сложности производства и количества стоящих вопросов, будет недостаточно. Весь набор инструментов будет обязательно реализован в дальнейшем.
Главные трудности — неприятие изменений персоналом
Главная трудность на пути внедрения технологий бережливого производства — нежелание работников выходить из зоны комфорта, чтобы воспользоваться предлагаемыми инновационными инструментами, считает руководитель технопарка «Юг-Мет» Евгений Коняхин. Проблема решалась через системное администрирование и вовлечение персонала в совместное решение текущих задач производства.
Стоит отметить, что в рамках проекта 11 сотрудников «Юг-Мета» прошли обучение по программе «Лидеры производительности». Теперь они могут самостоятельно внедрять новые стандарты на предприятиях.
По словам Евгения Коняхина, РЦК предлагает под новым углом взглянуть на производственные процессы, а также повышает вовлеченность трудового коллектива в решение текущих задач.
Источник: ЭкспертЮг